In 2016, I authored an AIA CES Course titled “Passive Housing: Affordable Fenestration Solutions”. It showed the difference in material costs and efficiencies in building to Passive House standards. Since then, materials used in the construction of both residential and commercial projects have become more available.
As demand grows for passive buildings, so does the emphasis on high-efficiency building materials. The high performance of windows and doors is essential to achieving the standard for passive construction as well as insulation, HVAC, and sealing techniques.
Passive House buildings provide a high level of occupant comfort while using very little energy for heating and cooling. They are built with meticulous attention to detail and rigorous design and construction according to principles developed by the Passive House Institute US or the Passivhaus Institute in Germany and can be certified through an exacting quality assurance process.
Many of the materials we once used in Passive House Construction in the US were imported from Europe and the lack of availability and selection resulted in a higher cost. Now Energy Recovery Systems, Insulating Materials, Sealing Tapes, and Energy Efficient Windows which are Passive House suitable are now all available in the US.
Residential Passive House
In one case study, The Scranton House is a residential example of a cost-effective home. This is a 2,153 square foot home which received the 2017 Passive House of the Year amongst other awards. It is a simple design which is key to being cost-effective. To be fair, the more elaborate the design with more corners and increased size would add to the cost of residential construction.
This home was built for $165 per square foot with a standard built to code residential home costing $175 to $200 in the same area. In a built to code residential home, the average energy cost would be $233 per month compared with the realized energy cost of $67 per month with The Scranton House.
Again, without the simple design and modest size, the cost could be 10-15% more than a conventional house. Savings on utility bills will usually completely offset this in just a few years. The design, positioning, and planning make for the most bang for your buck. Not to mention constant cleaner fresh air, quieter, consistent temperature, increased comfort level, and a mold-free environment are exceptional benefits of this form of construction.
Now let us look at commercial Passive House
According to PHIUS (Passive House Institute US) Many experienced Commercial Passive House Builders report premiums of 2% in building costs. That is a big reduction in labor and material costs compared to a 30% premium 15 years ago. Unlike residential, construction costs on larger projects can be reduced.
With the efficiency of skilled Passive House builder’s installation practices along with the availability of Passive House suitable materials, the commercial sector has increased exponentially. This has been in the multi-family and office-building sectors. Fueled by reduced maintenance and energy costs, building owners see the benefit in reduced operating costs.
There are now multiple projects finished and on the books that keep exceeding previous records. Park Avenue Green in the Bronx was the largest affordable multi-family in the US (2018). Bright Power worked with PHIUS to source specific project components from local manufacturers, reducing first costs for construction while still meeting strict performance requirements.
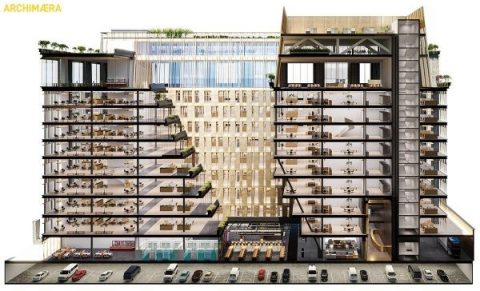
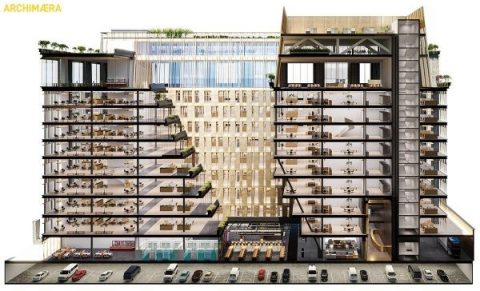
Elevation diagram of The Oasis – Archimæra
Long Island City is getting what JNY Capital, and United Hoisting Company say will be the largest office building in the US designed to passive house standards. “THE OASIS” will be a 425,000-square-foot spec office The Oasis is targeting biotech, life sciences, media, engineering, commercial office, and retail tenants. Initial office rents will be in the $40-$50 psf range, less than half of comparable space in Manhattan. Building owners will be able to sell at this price due to projected building costs using prefab construction techniques as well as anticipated energy savings.
The current largest Passive House building in the world is the Second + Delaware Apartments in Kansas City, Missouri. This project realizes 80-90% less energy than conventional buildings and has superior indoor air quality. This project was built to last 200+ years, features urban farming on the roof, 20% affordable housing, a $4 per sf lower first cost, and a 19% total lower lifecycle cost than stick built multifamily buildings.
In conclusion, Passive House standards not only save money over the long term, especially in light of rising energy costs, but are remarkably affordable to begin with. The investment in higher quality building components required by the Passive House standard is mitigated by eliminating expensive heating and cooling systems and streamlined construction techniques.